Precision is very important for every HDPE fitting fabrication welding machine project. You need exact joints to stop leaks and make strong pipelines. Reports say that precise welding tools, like the MM-Tech hdpe fitting fabrication welding machine, give better welds and fewer problems. Studies in the field show that careful control of welding settings makes the joints bend better and get stronger, so they break less. If you pick the right fitting and use advanced controls, you will get strong and dependable results.
Key Takeaways
Set the machine exactly right and line up the pipe well to make strong, leak-free HDPE pipe joints.
Check all materials closely and set up the welding machine the right way to stop weak spots and welding mistakes.
Watch the welding process carefully with digital controls and sensors to find problems early and keep the work good.
Follow safety rules and use the machine’s safety parts to keep yourself and your tools safe.
Keep good welding records with data tools to show quality and help with later projects.
Precision in HDPE Welding
What Precision Means
Precision in HDPE welding means you control each step. You make sure every pipe lines up just right. You set the temperature and pressure for butt fusion. Using a machine like the MM-Tech fitting fabrication welding machine helps you do this. You can control the settings exactly. This lets you make joints as strong as the pipe. You avoid mistakes that cause weak spots or leaks. Precision also means you follow rules for high-density polyethylene welding, like DVS or ISO guidelines. These rules help you get the best results every time.
Tip: Always check your machine settings and pipe alignment before you start. Even small mistakes can cause big problems later.
Why It Matters
Precise welding gives you joints that do not leak. When you use butt fusion on HDPE pipes, you heat and press the ends together. You do this under careful control. This makes a joint as strong as the pipe. You use fewer fittings, so there are fewer places for leaks. Studies show that precise welding makes the system last longer. It also needs less fixing. For example, a study on big HDPE pipes showed that careful control of welding pressure and temperature made the pipes stronger and tougher. Fusion welds help pipes stand up to chemicals and temperature changes. This means they work well in hard places. When you follow the right steps, you save money and time. Your pipes stay strong and work well.
Benefits of precise HDPE welding:
Fewer leaks and repairs
Better performance in harsh conditions
Lower maintenance costs
Preparation Steps
Material Inspection
Before you start welding, you need to check your materials. Good results depend on the quality of your pipe and fitting. You should follow industry standards for every inspection. Here are some important checks:
Test the raw material for density, melt flow rate, and oxidation induction time. This helps you know the resin quality.
Watch the pipe during production. Check its size and look for any surface problems.
Test the finished pipe for hydrostatic pressure, burst pressure, and impact resistance. You also need to check for environmental stress crack resistance and long-term strength.
Test each batch to make sure every pipe meets the same standards.
Look for third-party certification. This shows your pipe meets rules like ISO 4427, ASTM F714, or AWWA C906.
Make sure trained and certified people do the welding. They should follow standards like ASTM F2620.
Tip: Careful inspection helps you avoid weak spots and leaks in your hdpe system.
Machine Setup
Setting up your welding machine the right way helps you get strong, reliable joints. Follow these steps to prepare your equipment:
Check that your welding machine works well. Look at the power supply, voltage, cables, and connectors.
Pick the right welding process for your hdpe pipe and application.
Make sure your pipe and fitting match. This prevents welding problems.
Clean the joint area. Remove dirt and oil so the weld stays strong.
Set the welding parameters. Adjust voltage, current, and time based on the pipe’s needs.
Calibrate the machine before you start. This keeps your welds accurate.
Watch the welding process on the display. Check voltage, current, and time as you work.
Let the joint cool by itself. Do not move the pipe until it is ready.
Inspect the weld after cooling. Look for any defects or weak spots.
Keep your machine in good shape. Clean, inspect, calibrate, and store it properly.
Note: Careful setup and regular checks help your machine last longer and keep your welds strong.
HDPE Fitting Fabrication Welding Machine Operation
Alignment and Clamping
You start every welding job by making sure your pipes and fittings line up perfectly. The hdpe fitting fabrication welding machine helps you do this with strong clamps and a divided work table. You place each pipe on the table and use the clamps to hold them steady. The divided table lets you move the left and right sides separately. This makes it easier to mill the pipe ends flat and smooth. When you align the pipes, you avoid gaps and make sure the butt fusion joint is strong.
The MM-Tech machine uses a dual hydraulic system. This system gives you better control when you clamp and move the pipes. You can adjust the pressure for each side. This helps you get a perfect fit every time. Good alignment and clamping stop leaks and weak spots from forming in the joint. You also save time because you do not need to fix mistakes later.
Tip: Always check that the pipe ends touch evenly before you start the fusion process. Even a small gap can cause a weak weld.
Butt Fusion Machine Controls
You control the butt fusion machine with a simple color screen display. The MM-Tech models come in both hydraulic and CNC versions. The CNC models let you set the welding steps with just a few taps. You can choose the right settings for each pipe size and fitting. The machine follows the DVS standards, so you know you are using the best process.
The automatic butt fusion process uses a German motion sensor. This sensor checks the movement of the heater and cutter. It makes sure the pipes heat up and join at the right time. You can see all the steps on the screen. The machine also has a stop button that lets you pause or stop the process right away if you need to. This keeps you safe and protects your pipes.
The MM-Tech butt fusion machine supports many pipe sizes. You can work with pipes from 315mm up to 1200mm. Models like SWT-MA315, SWT-MA400, SWT-MA450, SWT-MA500, SWT-MA630, SWT-MA800, SWT-MA1000, and SWT-MA1200 cover a wide range. CNC versions can handle even more sizes, from 90mm to 1600mm. This means you can use the same machine for many jobs, from small fittings to large pe pipe butt fusion projects.
Here is a table showing some key benefits you get from using a modern butt fusion machine:
Performance Indicator / Benefit | Description / Validation |
---|---|
Fusion welding creates strong, leak-proof joints, making your system more reliable. | |
Corrosion resistance | HDPE pipes do not rust or corrode, so your joints last longer. |
Flexibility | Pipes can bend, so they work well in places with shifting soil. |
Long service life | Pipes can last up to 100 years if you use the right fusion process. |
Reduced maintenance costs | You spend less on repairs because the joints stay strong. |
Cost-effectiveness | You save money over time with fewer repairs and easy installation. |
Operational pressure capacity | Pipes can handle high pressure, up to 25 bars. |
Smooth internal surface | Water flows easily, and you avoid blockages. |
Fusion welding precision | You get strong bonds when you control temperature and pressure. |
Installation ease | Lightweight pipes and fittings make your job faster and easier. |
Monitoring Welds
You need to watch the fusion process closely to get the best results. The MM-Tech hdpe fitting fabrication welding machine helps you do this with real-time monitoring. The color screen shows you the temperature, pressure, and time for each weld. The German motion sensor tracks the movement of the heater and cutter. If something goes wrong, the machine can stop right away. This helps you fix problems before they cause defects.
You can also save and print welding data using the USB port. This lets you keep records for every job. You can check the data later to make sure each weld meets the standards. Weld tracking systems help you find and fix problems early. They also let you prove the quality of your work years later.
Here is a table showing how monitoring welds improves your results:
Metric | Benchmark | Impact |
---|---|---|
Welding Defect Rate | Reduction by 20% | You get fewer defects and better weld quality. |
On-Time Delivery Rate | Above 95% | You finish jobs faster and keep your clients happy. |
Equipment Utilization | Around 85% | You use your machine more and waste less time. |
Customer Satisfaction | 80-90% | More clients trust your work and come back for more jobs. |
Employee Productivity | High output | Your team works faster and makes fewer mistakes. |
You can also use non-destructive testing, like ultrasonic testing, to check your welds. Sensors and IoT tools help you watch the fusion process in real time. This means you can spot problems early and avoid costly repairs. When you use these tools, you make sure every pipe and fitting meets the highest standards.
Note: Good monitoring and record-keeping help you build a strong reputation for quality and safety in every hdpe project.
Key Features for Precision
Digital Controls
Digital controls make it easier to use your welding machine. You can set the temperature, pressure, and time for each weld. This helps every pipe joint stay strong and safe. The MM-Tech hdpe fitting fabrication welding machine has a color screen and CNC system. You can see each welding step and change settings quickly.
Digital controls let you watch the welding process as it happens. In shipbuilding, experts use digital data to check welding information right away. They use smart computer programs to guess and improve weld quality. These programs work faster and better than old ways. One study showed a digital control system kept the welding current steady. This helped lower mistakes and made welds more stable.
You can find more benefits of digital controls in the table below:
Feature | Benefit | Example Outcome |
---|---|---|
Real-Time Data Analysis | You can watch welding numbers and change settings for better results. | Productivity went up by 15%. |
Documentation & Traceability | The machine saves records for each weld, making checks easy. | Paperwork mistakes dropped by 20%. |
Quality Validation | Digital tools check welding settings for every pipe. | Weld problems dropped by 30%. |
Equipment Monitoring | The system checks machine health and warns you about trouble. | Downtime went down by 40%. |
Tip: Use digital controls to set the right numbers for each pipe size. This helps you avoid mistakes and get strong welds.
Safety Systems
Safety matters a lot when you weld pipes. The MM-Tech machine has many safety features to protect you and your work. The dual hydraulic system gives you better control over clamping and moving each pipe. This helps you line up the pipes just right before welding. The stop button lets you stop the machine fast if something goes wrong.
The divided work table lets you move each side by itself. This makes it easier to get the pipe ends ready for welding. Buffering devices on each oil cylinder help stop sudden moves that could hurt the pipe or machine. The automatic cutter stop keeps you safe by stopping the cutter when it is done.
You can use sensors to watch the welding process. These sensors check the heater and cutter for temperature and movement. If the machine finds a problem, it can stop to keep you safe. These safety systems help you make strong, leak-proof joints and protect your equipment.
Note: Always check the safety systems before you start. Good safety features help you avoid accidents and keep your pipes working well.
Data Management
Good data management helps you keep track of every weld you make. The MM-Tech machine lets you save welding data to a USB drive. You can print the data or use it to check your work later. This makes it easy to show your pipe joints meet industry rules.
Researchers use special tests to check how strong welded pipes are. They measure how much force it takes to break a weld. They also see how the weld holds up in different situations. By saving and checking your welding data, you can find small problems early. You can also use the data to make your welding better over time.
The machine’s data management system helps you follow rules and pass checks. You can show inspectors that every pipe joint meets the right standards. This builds trust with your clients and helps you get more jobs.
Benefits of strong data management:
Easy record-keeping for every pipe weld
Fast checks for quality and safety
Better planning for future projects
Proof of following industry rules
Tip: Use the USB data export to back up your welding records. This helps you stay organized and ready for any check.
MM-Tech’s Commitment to Quality
MM-Tech gives you a 24-month warranty and 24/7 after-sales service. You get help whenever you need it. Over 3,000 customers in more than 100 countries trust MM-Tech for their pipe welding needs. When you pick MM-Tech, you get a machine that gives you precision, safety, and reliability for every project.
Troubleshooting and Tips
Common Issues
You may face several challenges when working with a pipe welding machine. Industry reports show that some problems happen more often than others:
Many businesses find that the high cost of advanced welding equipment can be a barrier, especially for smaller companies.
A shortage of skilled workers often leads to poor welds. This can make pipe joints weak and less durable.
Some machines do not fit every pipe size or type. This can slow down your project and increase costs.
Complex machines need regular maintenance. If you do not have trained staff, you may see more downtime and higher expenses.
Tip: Always check your machine’s compatibility with the pipe you plan to use. Make sure your team has the right training before starting any butt fusion job.
Best Practices
You can avoid many problems by following proven steps. Successful projects use these best practices:
Keep the heating temperature between 400°F and 450°F. This range helps you get a strong, even weld.
Use steady, calibrated pressure during welding. This prevents gaps and makes the joint stronger.
Choose automated equipment with sensors and data logging. These features help you track temperature, pressure, and time in real time.
Align pipe ends exactly. Use clamps or laser tools to make sure the fit is tight.
Watch for changes in the environment. Use tents or shields to keep the welding area stable.
Run test welds before you start the main job. This helps you check your settings and avoid mistakes.
A recent case study shows that using advanced testing, like phased array ultrasonic testing, helps you find hidden defects in the weld. This method checks the whole weld and finds problems that older tests might miss. By using these tips, you can make sure your pipe joints stay strong and last longer.
Note: Good preparation and careful monitoring help you get the best results from every hdpe pipe welding project.
You can get very accurate results with your HDPE fitting fabrication welding machine if you follow simple steps. Change the machine’s speed, temperature, and how the pipes line up for each weld. Use special features to make the welds stronger and have fewer mistakes, like you see in the table below.
Metric | Result |
---|---|
Weld strength | 130% of base material |
Leak-proof welding rate | 99.9% |
Defect rate reduction | 30% |
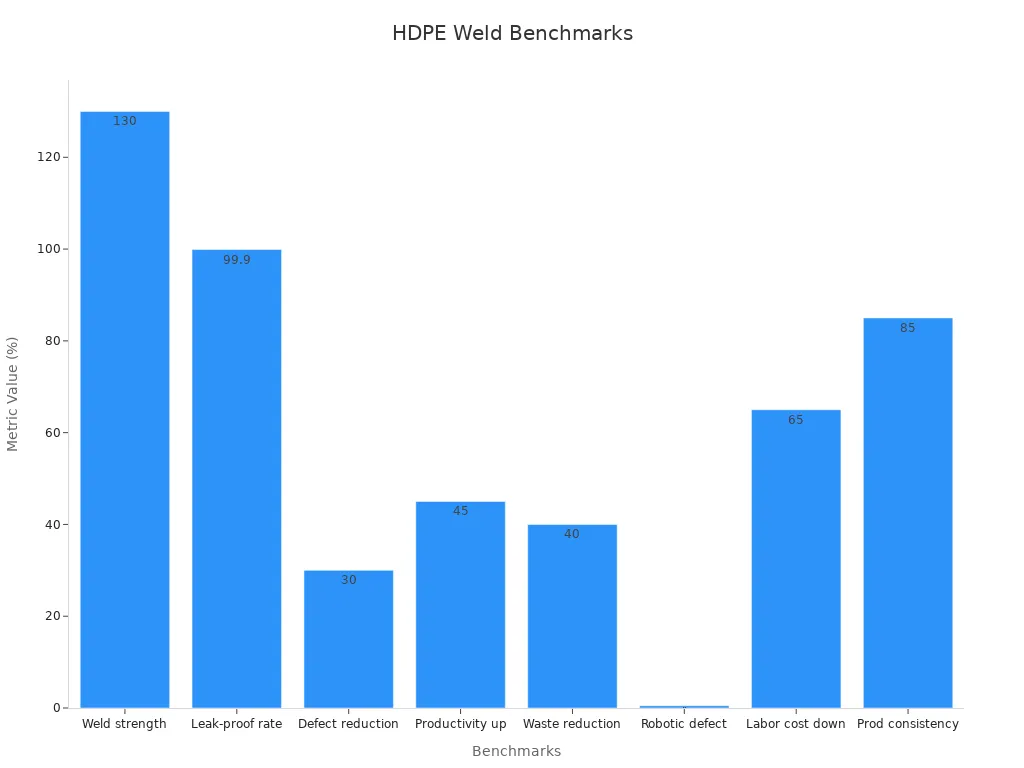
Tip: Make a short checklist for setup, lining up, and watching the weld.
Keep learning new things and use help from after-sales support. Training often and keeping welder logs help you stay good at your job and meet quality rules.
Welder logs show your skills and tests.
Certifications and audits show you keep learning.
Recertification and training help you stay current.
FAQ
How do you choose the right HDPE fitting fabrication welding machine size?
You should match the machine’s supported pipe diameter to your project needs. For example, MM-Tech machines cover sizes from 90mm to 1600mm. Always check your pipe size before you start.
What safety steps should you follow during welding?
You must check all safety systems before welding. Use the stop button if you see a problem. Wear gloves and eye protection. The machine’s sensors and automatic stops help keep you safe.
How can you keep your welding machine in good condition?
Clean the machine after each use. Inspect cables and connectors for damage. Calibrate the controls often. Store the machine in a dry place. Regular care helps your machine last longer.
Why is saving welding data important?
Saving welding data helps you track each job. You can use a USB drive to export records. This makes it easy to show inspectors your work meets industry standards.
Tip: Always back up your welding data. This helps you solve problems faster and keeps your records safe.