Trailer butt fusion welding machines are special because they have strong trailers and new features. These machines can go right to where people are building things. They give workers power and tools at the job site. The machines have their own systems, parts you can take off, and easy-to-use controls. This makes welding fast and works well every time. Safety parts like jaws with teeth and brakes that lock by themselves keep each weld safe. MM-Tech is a top company. They make new welding tools that help workers who need machines they can trust for every job.
Key Takeaways
The Mazinger 630i trailer welding machine is simple to move. It works well in small or rough spots. This helps teams start work fast.
Smart controls and automation make welding quicker. They help lower mistakes. They keep every weld strong and safe.
Strong safety features and a tough design protect workers. They make sure every weld is high quality.
The machine can weld many kinds and sizes of plastic pipes. This makes it good for many types of projects.
Using this machine saves time and lowers hard work. It tracks every weld. This helps teams work better and finish jobs faster.
Portability
Trailer Design
MM-Tech made the Mazinger 630i easy to move. The trailer butt fusion welding machines have a tough trailer frame. Workers can take the machine from one place to another. The trailer helps teams get to far or hard-to-reach spots. One big feature is the removable chassis. Workers can take off the chassis and use the machine in a trench or on bumpy ground. This makes the machine helpful for many building jobs. The strong frame keeps the machine safe when moving or working. It protects all the main parts, even on rough roads or busy sites. These features help workers set up the machine faster and with less work.
Tip: The trailer design helps teams start welding soon after they get to the site.
On-Site Flexibility
The Mazinger 630i is special because it is flexible on the job. Workers can set up the machine almost anywhere they need. The removable chassis lets them put the machine close to the pipes, even in tight spaces. This means workers do not have to lift or move heavy pipes as much. The strong frame and tight jaws keep the pipes still during welding. These things make welding safer and more steady. Teams can work quicker and make fewer mistakes. The machine works well in many places, like city roads or far-off fields. With these features, workers can finish jobs on time and do good work.
Integrated Systems
All-in-One Controls
The Mazinger 630i is special because it has smart systems. It uses a SIEMENS PLC system to control the fusion process. This system checks temperature, pressure, and timing very carefully. Workers see a simple screen that is easy to use. The screen helps workers follow each step, so nothing is missed. The control panel can be taken off and moved. Workers can put it in a safe place or near the fusion area. The screen also saves data, so teams can keep up to 30,000 fusion reports. These features make the Mazinger 630i simple to use, even for new workers.
The hydraulic trimmer is another important part. It gets pipe ends ready by making them smooth and flat. This step helps make strong fusion joints. The trimmer works with the easy screen, so workers use just a few buttons. These things help workers set up fast and start welding right away.
Efficiency in Operation
The Mazinger 630i’s smart systems help jobs go faster. The SIEMENS PLC system runs the fusion process by itself. This means workers make fewer mistakes. The easy screen gives clear steps, so no one has to guess. The machine keeps each weld the same, so they are strong and safe.
Automated controls help stop mistakes from happening.
Teams can watch the process and check the quality.
The machine holds pipes tight and lines them up right.
Automation makes each weld take only about 5 minutes.
The easy screen helps workers feel less tired and confused.
Good welds mean less fixing and less wasted time.
The machine meets tough rules for safety and strength.
The Mazinger 630i’s easy features and smart tools help teams finish work quickly. Workers fix fewer mistakes and make strong welds. The easy screen and strong tools make this machine a great pick for anyone who needs good fusion welding on site.
Safety & Durability
Robust Construction
The Mazinger 630i is built to be very strong. It uses a frame made from welded steel tubes and tough aluminum. This makes the machine stable and hard to break. The design spreads out the welding force so nothing breaks. This helps every weld come out right. The machine has a chassis you can take off. This makes it safe to use in trenches or on bumpy ground. Outriggers and hydraulic clamps keep the machine steady while working. The trimmer is big and uses an electric motor and hydraulics. It gets pipes ready with care. All these parts work together for good results and long life.
Welded steel tube frame gives strength
Removable chassis keeps trench work safe
Hydraulic pipe lifts help workers lift less
Strong jaws and inserts stop pipes from slipping
Rugged outriggers keep the machine steady
The Mazinger 630i is made for safety and quality. It is a good choice for tough job sites.
Safety Features
Safety is very important in the Mazinger 630i. The heating plate has a frame and shield to protect workers. This stops burns and keeps heat under control. It also helps stop overheating. The dual-axis frame and guide rails make the machine stable. This helps workers get good welds every time. Strong jaws hold pipes tight so they do not slip. The control panel can be moved. Workers can watch the process from a safe spot.
MM-Tech gives training and certificates to workers. The training teaches how to use the machine and stay safe. Workers learn to check the machine and use safety gear. They also learn the best ways to work safely and well.
The Mazinger 630i follows ISO 21307 and ASTM F2620 rules. These rules make sure welds are safe and strong. By following these rules, the machine gives good results and keeps workers safe.
The Mazinger 630i brings safety, quality, and accuracy together. Its features help teams do good work and stay safe.
Versatility
HDPE and Plastic Pipe Butt Welding Machine
The Mazinger 630i is a very useful plastic pipe butt welding machine. It can join pipes made from hdpe, PE, PP, and PVDF. The machine works with pipe sizes from 315mm to 630mm. This lets teams do many kinds of welding jobs. The Mazinger 630i uses smart controls for heat, pressure, and time. These controls help workers make strong, leak-free joints each time. The trailer design means teams can take it anywhere they need. Workers use it in trenches, on rough ground, or at busy sites. The Mazinger 630i makes hdpe welding easy and safe. Its strong jaws and hydraulic lifts hold pipes steady while welding. The machine’s data logging system records every weld. This helps teams check their work and follow project rules.
Note: Keeping pipes and the machine clean is important for good hdpe welding. The Mazinger 630i helps workers keep things clean and safe.
Range of Applications
The Mazinger 630i plastic pipe butt welding machine works for many jobs. Teams use it for city water pipes, gas lines, mining pipes, and big building projects. Hdpe pipes are used a lot because they last long and do not break easily. The Mazinger 630i can weld hdpe pipes for city water lines. It also works for gas pipes in towns and country areas. Mining teams use the machine to join hdpe pipes for water or minerals. Construction crews use the Mazinger 630i for big jobs like bridges or tunnels. The machine can weld many pipe types and sizes, so it is a great choice for many jobs. Its strong build and simple controls help workers finish faster and make fewer mistakes. The Mazinger 630i gives teams what they need to handle any hdpe welding job on site.
Cost & Time Savings
Labor Reduction
MM-Tech’s trailer butt fusion welding machines help teams save time and money. The Mazinger 630i uses automation to run the fusion process. Workers do not have to do as many jobs by hand. The machine controls temperature, pressure, and timing with one button. This helps stop mistakes and keeps the job safe. The hydraulic trimmer and removable chassis make setup simple. Workers do not spend much time lifting or moving pipes. The chart below shows how these machines help workers do better and faster work:
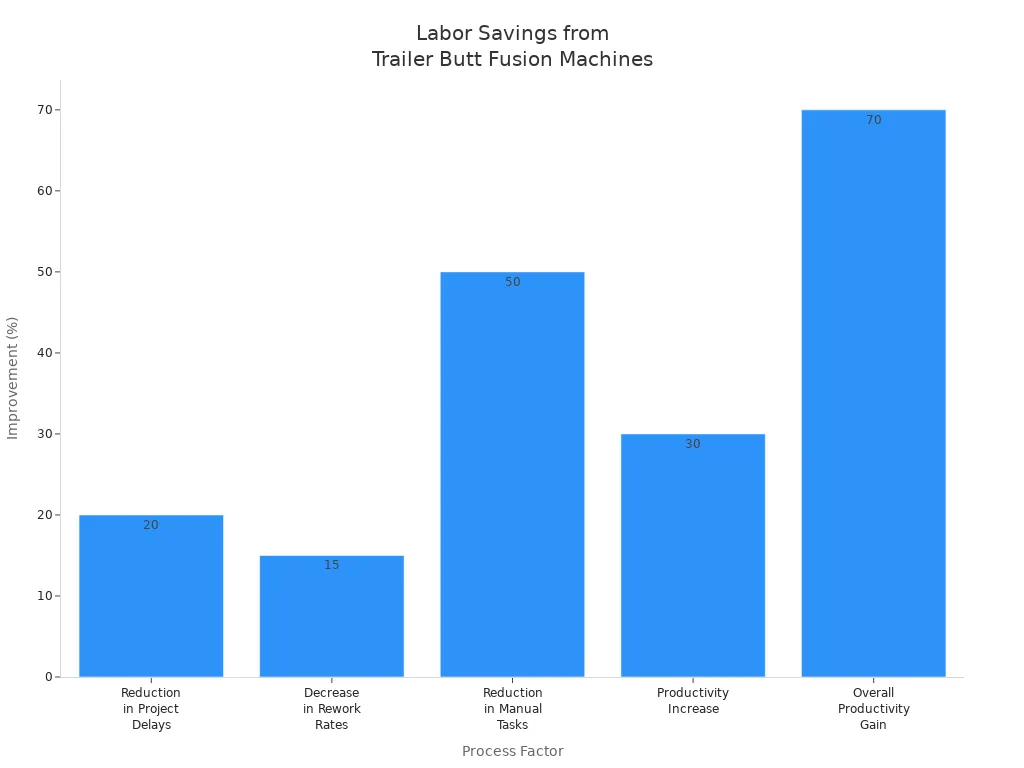
Process Factor | Improvement Impact on Labor and Efficiency |
---|---|
Reduction in Project Delays | 20% fewer delays, so teams wait less and work more |
Decrease in Rework Rates | 15% fewer fixes, so workers do not redo jobs as much |
Reduction in Manual Tasks | 50% less hand work, so workers save energy |
Productivity Increase | Up to 30% more welding done, so jobs finish faster |
Overall Productivity Gain | Up to 70% better results, so teams save time and effort |
Project Efficiency
The Mazinger 630i is easy to move to any job site. Teams can set it up fast and start welding right away. This helps finish projects sooner. The strong trailer and simple controls let workers weld hdpe pipes almost anywhere. Workers do not waste time waiting or moving tools. The Mazinger 630i lets teams do more fusion jobs each day. Companies say welding is up to 50% faster and labor costs are 30% lower than with hand tools. The tough parts and two-year warranty help cut repair costs and downtime.
Data Logging
Automated data logging is an important part of new hdpe pipe fusion welding machines. The Mazinger 630i saves every weld, including temperature, pressure, and time. This helps teams check their work and follow safety rules. The machine can keep up to 30,000 welding reports and send them out by USB. Some benefits of this system are:
Teams can check quality right away and spot mistakes early.
The machine makes ISO weld certificates by itself.
There is less paperwork and audits are faster.
The machine is used better and there is less waiting.
Customers trust the work because records are clear.
The Mazinger 630i gives teams a way to track every hdpe fusion weld. This means better work, more jobs done, and safer projects.
MM-Tech’s trailer butt fusion welding machines are known for being strong and safe. They also have smart controls that are easy to use. The Mazinger 630i gives workers:
Joints that do not leak and can handle pressure changes
Controls that work well even in tough places
Parts that last a long time and a two-year warranty
Quality that is checked and meets world standards
Project teams can count on MM-Tech for help and answers that fit their needs. Picking the Mazinger 630i means you get a machine that works well, saves time, and gives good results on every job.
FAQ
What makes trailer butt fusion welding machines different from other welding equipment?
Trailer butt fusion welding machines are easy to move. They have simple controls for workers. Teams can bring the machine right to the job site. These machines make strong welds on hdpe and other plastic pipes. The welds are neat and last a long time.
Can the Mazinger 630i handle different pipe materials and sizes?
The Mazinger 630i can weld hdpe, PE, PP, and PVDF pipes. It works with pipe sizes from 315mm up to 630mm. This means teams can use it for many kinds of jobs. The machine helps finish lots of fusion projects.
How does the machine ensure safety and quality during welding?
The Mazinger 630i has a dual-axis frame and insulated heating plate. It also uses strong jaws to hold pipes tight. The controls are easy to use and help workers do a good job. The machine follows ISO and ASTM rules for safe welds.
Are the controls easy for new users to learn?
The controls are simple and the screen is clear. The machine shows each step to help new users. Even people who have not welded before can use it. They can make strong and safe welds with this machine.
What are the main benefits of using this machine on construction sites?
Teams save time and do less hard work with this machine. The Mazinger 630i sets up fast and welds pipes well. It also keeps track of each weld with data logging. These things help teams work better and finish jobs faster.